
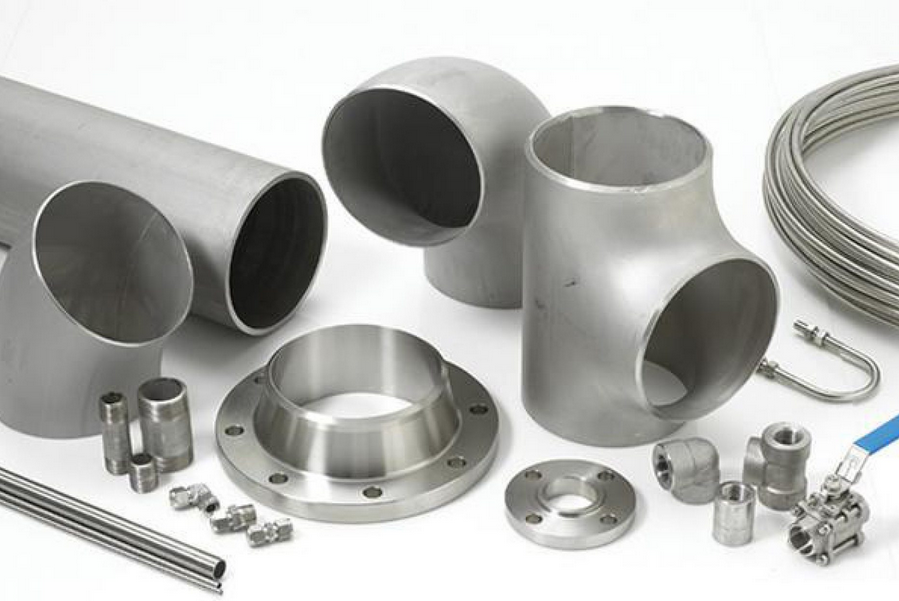
The wire cutting method, this method can meet the incision quality requirements. However, it should be noted that the stainless steel pipe will change its color after it is cut, and it must be polished and polished. The processing speed is very slow, and production hours can be used. area, the height of the residual area constitutes the surface roughness.Let’s take a look at the carbon arc gouging. This method actually uses a graphite rod or an arc generated between a carbon rod and a workpiece to melt the metal and blow it off with compressed air to achieve processing of the grooves on the surface of the stainless steel pipe. method. However, carbon arcs produce smoke, dust, and arc radiation. The inner wall of the stainless steel pipe is easily accompanied by a large amount of melted and cooled metal residue, which is difficult to remove. Other factors: In addition to the above reasons, the reasons for the rough and uneven processing surface are: the extrusion friction marks caused by the wear on the back of the tool the defects on the blade are reflected in the groove marks on the processing surface chips and scratches.Īccording to the summary of stainless steel pipe manufacturers, it is found that when cutting stainless steel pipes, due to the geometric shape, geometric parameters, feed motion, and roughness of the cutting edge itself, the material layer on the processing surface cannot be completely removed, leaving residue on the processing surface. Vibration not only has a great impact on tool wear but also deteriorates the surface quality of processed stainless steel pipes.Ĥ. The height of the vibration wave is related to the amplitude, the density of the vibration line, and the vibration frequency. The vibration lines are distributed longitudinally, transversely, or obliquely. Vibration is generated during the cutting process, causing vibration lines on the processed surface. Vibration is caused by too much radial cutting force or too little rigidity of the workpiece system. Vibration: If there is vibration during the cutting process, vibration lines will appear on the processed surface, and the surface roughness will increase significantly.
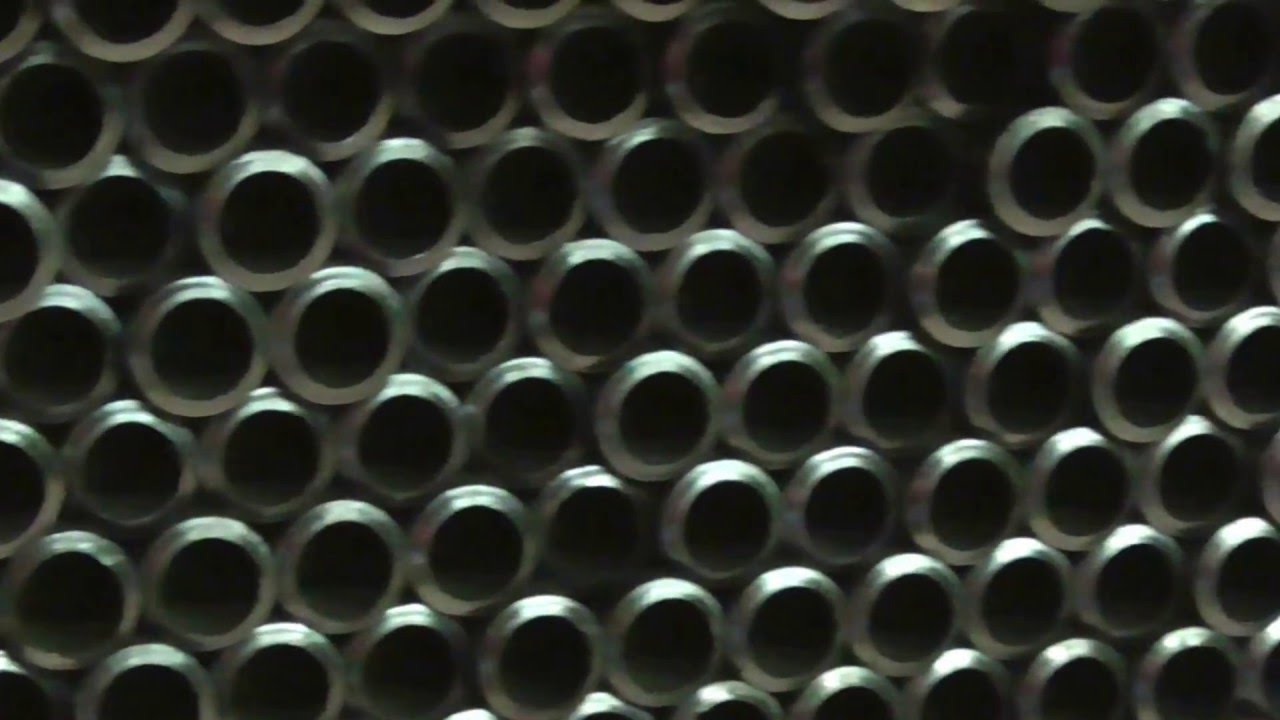
Scales have a serious impact on the quality of the processed surface, often reducing the surface roughness level of stainless steel pipes to 2~4.ģ.
#CUT STAINLESS STEEL PIPE CRACK#
When the cutting force exceeds the adhesive force When cutting, the chips flow out and cut, and the crack guide layer remains on the machined surface to form scales. The reason for the scale is that during the cutting process, the chips and the surface of the front knife have severe friction, and under the extrusion of the accumulated adhesive layer, the plastic deformation of the metal layer is exacerbated, causing the processed surface in front of the blade to crack. Scales: Refers to the scaly burrs on the processed surface. The influence of built-up edge on the surface roughness of stainless steel pipes has two aspects: ① longitudinal grooves can be carved ② when it is broken and falls off, it will also adhere to its own processing surface.Ģ. Under the huge pressure between the tool and the block, the cutting bottom and Cold welding of the front of the tool. Built-up edge: The generation of the built-up edge is due to the plastic flow of the block during the cutting process and the external friction between the tool and the block exceeds the internal friction. Today, stainless steel pipe manufacturers will briefly summarize the main reasons for these problems.ġ.
